Skurcz, odkształcenie i czas
InnovMetric i ShapeGrabber pomagają MPC Molder w podejmowaniu szybkich decyzji produkcyjnych dotyczących części samochodowych.
Ponieważ główne produkty firmy Miniature Precision Components (MPC) (tj. zawory PCV, złączki, rurki, zbiorniki płynów, korki wlewu paliwa itp.) stały się towarami o coraz mniejszych marżach zysku, MPC zaczęła oferować producentom samochodów nowe produkty; są to m.in. pokrywy silnika z wytłoczonymi logotypami. W przeciwieństwie do niemal całej dotychczasowej produkcji MPC, są to części o skomplikowanej formie: kopułkowe, tłoczone lub ryflowane. Mają one wpływ na wygląd: patrzą na nie kupujący w salonach sprzedaży.
Ponieważ części te były kilkakrotnie większe niż prawie wszystkie wcześniejsze produkty MPC, skurcz i odkształcenie stanowiły nowe i trudne wyzwania w zakresie zapewnienia jakości. Aby rozpocząć produkcję zgodnie z harmonogramem, inżynierowie musieli podejmować krytyczne decyzje dotyczące oprzyrządowania i procesu w bardzo krótkim czasie i przy zbyt małej ilości danych.

Same skurcze i odkształcenia mogą spowodować przekroczenie całego zakresu tolerancji. Nieuniknione różnice w procesie formowania sprawiają, że części jeszcze bardziej odbiegają od specyfikacji. Jak zawsze w przypadku producentów samochodów, czas jest podstawą relacji biznesowych. MPC daje sobie zaledwie cztery tygodnie od otrzymania formy na rozpoczęcie produkcji i dostarczenie próbek części.
Wymiary muszą mieścić się w zakresie tolerancji +/- 5 mm, uwzględniając wszystkie procesy, materiały i różnice w oprzyrządowaniu.
Skurcze i odkształcenia są niwelowane przez:
- Zmianę procesu formowania
- Zwiększenie tolerancji części
- Budowę urządzenia chłodzącego
- Modyfikację narzędzia do formowania części
Wybór i wdrożenie każdego z tych rozwiązań może zająć cztery tygodnie, przez co nie ma już czasu na rozwiązywanie kolejnych problemów. „Cztery tygodnie to jedyny czas, jaki mamy na ulepszenie i ustabilizowanie procesu formowania, a musimy uwzględnić nie tylko skurcz i odkształcenie” — mówi Clark.
Firma MPC rozwiązała swoje problemy ze skurczami i odkształceniami za pomocą skanera laserowego ShapeGrabber 3D oraz opartego na chmurze punktów oprogramowania pomiarowego PolyWorks® firmy InnovMetric Software. Dzięki świadomemu zarządzaniu MPC wykorzystała to rozwiązanie jako przewagę konkurencyjną: Krótszy czas wprowadzania na rynek i wyższy stopień zapewnienia jakości.
Wyzwanie
Dużą trudnością, z jaką borykają się producenci form w odniesieniu do skurczy i do odkształceń, są ich odrębne przyczyny. Skurcz jest związany z materiałem; wynosi od 2% do 14% i może się różnić między partiami żywicy. Odkształcenia związane są z chłodzeniem i stosowaniem przez konstruktora grubych i cienkich przekrojów. Sprostanie wyzwaniom dotyczącym wymiarów i tolerancji wymaga wielu analiz i obliczeń oraz lat doświadczenia.
Producenci form rozpoczynają projektowanie nowego narzędzia od szacunkowych wartości skurczu z karty charakterystyki żywicy. Aby poradzić sobie z odkształceniami, producenci form wykorzystują swoją wiedzę na temat bram, otworów wentylacyjnych i linii wodnych. Jednak dopóki narzędzie nie zostanie zbudowane i uruchomione, skurcz i odkształcenie stanowią jedynie założenia.
Pomiary stykowe, analiza przepływu w formie i fotogrametria zawiodły
Przed wprowadzeniem skanowania laserowego i inspekcji opartej na chmurze punktów, producenci form nie mieli narzędzi do inspekcji powierzchni, które byłyby zarówno wszechstronne, jak i szybkie. Najlepszymi dostępnymi metodami były pomiary stykowe za pomocą współrzędnościowej maszyny pomiarowej (CMM), analiza przepływu w formie oraz fotogrametria. Jednak wszystkie te metody okazały się nieskuteczne.
Pomiary stykowe
Pomiar stykowy pomija drobne nierówności, wgłębienia i, jak zauważył Clark, „bardziej subtelne aspekty, takie jak przesunięcie odkształcenia w skoku pary punktów X i Y, co powoduje wyskoczenie innego punktu poza tolerancję Z”. Dlatego też dokładne zbadanie powierzchni wymaga 500 000 trójwymiarowych (3D) punktów, a czasem miliona lub więcej, a nie kilkuset, zapewnianych przez pomiar stykowy.
Ponadto Clark mówi, że „maszyna współrzędnościowa potrzebuje siedmiu dni roboczych na ustawienia zadania, dwóch kolejnych dni na wykonanie pomiarów i kolejnych pięciu dni na opracowanie wszystkich danych. Ponieważ CMM są zawsze zajęte, być może będziemy musieli poczekać kolejne siedem dni na miejsce w kolejce. Tak więc za pomocą metody punkt po punkcie mamy w najlepszym wypadku tylko dwie próby”.
Analiza przepływu w formie
Analiza przepływu w formie to symulacja komputerowa, która przewiduje, jak żywica będzie się kurczyć i odkształcać na podstawie lokalizacji i wielkości bramek narzędzia. Ma ona trzy poważne wady:
- Wykorzystywane są wymiary nominalne, a nie rzeczywiste dane kontrolne z części; późniejsze zmiany formy ciężko uwzględnić.
- Przewidywania dotyczące odkształceń są jedynie teoretyczne i cyfrowe. Wyjście poza wirtualną sferę przepływu formy wymaga udoskonaleń, których producenci form mogą odmówić.
- Jak każda symulacja, analizy przepływu formy zawierają ukryte założenia i wartości liczbowe, które mogą nie mieć potwierdzenia w świecie rzeczywistym.
„Musimy wiedzieć, co faktycznie wydarzyło się w formie, a nie co miało się wydarzyć” — mówi Clark. Analiza przepływu w formie jest również kosztowna — do 12 000 USD na narzędzie — i zwykle zajmuje dwa z dostępnych czterech tygodni.
Fotogrametria
Fotogrametria to pomiar za pomocą fotografii o wysokiej rozdzielczości. Fotogrametria rejestruje powierzchnie kilkakrotnie większe niż skanery laserowe, ale do wyrównania mogą być wymagane przyklejone znaczniki. Po zdigitalizowaniu zdjęć można je łatwo porównać z pobranym plikiem CAD lub wgrać do pliku CAD jako łatę powierzchniową.
Fotogrametria została wypróbowana jako alternatywa dla uchwytów kontrolnych i mierników dla wiązek podciśnienia silnika. „Problemem inspekcji jest to, że są one różne dla każdego silnika” — mówi Clark. „W ciągu 13 lat, od kiedy tu pracuję, kupiliśmy ponad tysiąc mierników, które kosztowały łącznie jakieś 3,5 mln dolarów. Części są czarne, więc ciężko je sfotografować, o ile to w ogóle możliwe i zawsze mamy problemy z oświetleniem otoczenia i postrzeganiem głębi w osi Z” — dodaje.
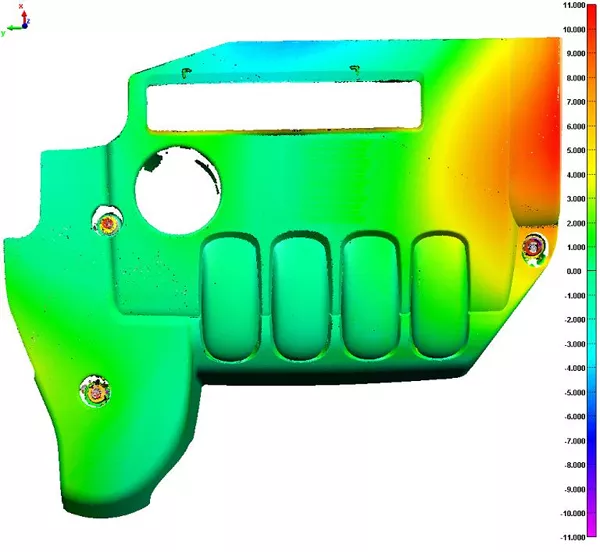
Mapa kolorów porównania danych do CAD
Rozwiązanie
Do inspekcji części plastikowych MPC wykorzystuje skaner ShapeGrabber Ai810C. Ten wieloosiowy skaner 3D umożliwia użytkownikowi wykonanie kompletnego skanu części jednym kliknięciem myszy: system zajmuje się resztą.
Ta łatwość obsługi wynika z zastosowania wielu osi skanowania (poziomej i pionowej), a także trzeciej osi obrotowej, na którą nakładana jest część. Wszystkie te osie są skalibrowane w tym samym układzie odniesienia, dzięki czemu wiele skanów jest wyrównanych automatycznie. Ustawiając z wyprzedzeniem wymagane skany dla danej części, można łatwo zautomatyzować proces skanowania.
Proces konfiguracji trwa zaledwie kilka minut ze względu na bardzo dużą głębię ostrości (DOF) głowic skanujących. Duża DOF pozwala na skonfigurowanie skanów za pomocą prostego i intuicyjnego graficznego interfejsu użytkownika, ponieważ nie jest konieczne ścisłe podążanie za złożonym konturem części, jak w przypadku większości innych skanerów.
Głowice skanujące pozyskują dane z prędkością 18 000–150 000 pkt/s, dzięki czemu wygenerowanie kompletnej chmury punktów przedstawiającej część zajmuje zaledwie kilka minut. Plik danych jest następnie przetwarzany przez PolyWorks|Inspector™ w celu zakończenia procesu inspekcji.
Połączenie szybkości i łatwości obsługi skanera sprawia, że jest on dostępny dla większej liczby użytkowników, a także skraca czas konfiguracji i inspekcji, znacznie obniżając koszty inspekcji w porównaniu z alternatywnymi metodami.
Dane potrzebne MPC są dostępne w ciągu 15 minut, a nie w ciągu kilku dni
Inspekcja oparta na chmurze punktów w programie PolyWorks
Inspekcje pokryw silnika w MPC są wykonywane z kolorowymi mapami tolerancji w PolyWorks|Inspector. PolyWorks porównuje miliony punktów danych uzyskanych przez skaner z modelem odniesienia CAD. Specjaliści MPC ustawiają tolerancje w programie PolyWorks, aby określić dopuszczalne i niedopuszczalne odchylenia między punktami danych a modelem CAD. Wyświetlacz wykorzystuje całe spektrum kolorów od czerwonego (tolerancja dodatnia, za dużo materiału) do niebieskiego (tolerancja ujemna, za mało materiału). Ponieważ zakres tolerancji mapy kolorów można ustawić, jest to doskonałe narzędzie do analiz warunkowych typu „co jeśli”. „Dzięki mapom kolorów możemy zobaczyć, co tak naprawdę dzieje się wewnątrz formy, na które powierzchnie wpływa zmiana tolerancji i o ile” — wyjaśnia Clark. „To, co naprawdę pokazuje nam mapa kolorów” — dodaje — „to sposób, w jaki plastikowa część unosi się wewnątrz formy. Wiemy, że materiał części skurczy się do właściwych wymiarów, a odkształcenie podczas chłodzenia doprowadzi do kształtu, o który chodziło projektantowi”.
Jeśli inżynierowie MPC muszą sprawdzić coś, co nie zostało początkowo określone w układzie inspekcji, po prostu klikają punkt w danych lub dodają punkty poprzez ponowne skanowanie. W obu przypadkach trwa to zaledwie kilka minut. W przeszłości wymagało to przeprogramowania maszyny współrzędnościowej. „By dodać choćby jeden punkt sprawdzany dotykowo, trzeba było zaczynać wszystko od nowa” — mówi Clark. „Nigdy nie trwało to krócej niż dwa dni”.
Dla użytkowników w MPC i jej klientów, ShapeGrabber i PolyWorks to jedyny system, który zapewniał:
- Nadążanie za tempem produkcji i częstotliwością inspekcji
- Przeprowadzanie standardowych testów powtarzalności i odtwarzalności (R&R), które certyfikują systemy inspekcji
W teście R&R operator trzykrotnie mierzy cechę na 10 częściach. Następnie drugi operator mierzy tę samą cechę na tych samych 10 częściach jeszcze trzykrotnie, po czym porównuje się wyniki. PolyWorks i ShapeGrabber pomyślnie przeszły te testy.
Wszystkie inne metody oparte na laserach były zbyt wolne. Żadna z nich nie potrafiła zebrać niezbędnych danych w czasie krótszym niż dwie lub trzy godziny.
„Skanowanie dostarcza nam wszystkie dane dotyczące powierzchni, których potrzebujemy, aby wybrać opcję produkcyjną, w ciągu kilku minut, zamiast dwóch lub trzech tygodni” — mówi Clark. „Otrzymujemy wyrównanie i formatowanie z PolyWorks w czasie bardzo zbliżonym do rzeczywistego. Wreszcie mamy wystarczająco dużo czasu, aby podjąć trudne decyzje dotyczące produkcji”. Dodaje: „Ponieważ możemy tak szybko zebrać wszystkie potrzebne nam dane dotyczące wymiarów i tolerancji, zostaje nam kilka dodatkowych dni na opracowanie i analizę każdego zlecenia. Ten dodatkowy czas jest bardzo przydatny przy podejmowaniu decyzji dotyczących zwiększenia zakresu tolerancji, modyfikacji narzędzia, zmiany procesu lub zlecenia wykonania oprzyrządowania chłodzącego”.
Dzięki oszczędności czasu inżynierowie mogą dokonać ponownego przeglądu. Może on obejmować podejrzane obszary w nowej partii części próbnych. „ShapeGrabber i PolyWorks pomagają nam w całym procesie konfiguracji” — stwierdza Clark.
„Uważamy, że dzięki ShapeGrabber i PolyWorks firma MPC osiągnęła dwutygodniowy zwrot z inwestycji (R-O-I)” — dodaje. „Zyskaliśmy dwie nowe przewagi konkurencyjne: bezkompromisowe zapewnienie jakości i szybkie rozpoczęcie produkcji. Dzięki skanowaniu 3D i inspekcji opartej na chmurze punktów mamy teraz kilka dodatkowych dni na podjęcie ważnych decyzji biznesowych. ShapeGrabber i InnovMetric pomogły nam w całym procesie konfiguracji” — mówi Gregory Clark.
Korzyści
Sukces na nowym, wymagającym rynku
Prawdziwym testem efektywności nowej technologii jest to, czy jej korzyści wykraczają poza potrzeby użytkowników w ich codziennej pracy. W większym przedsiębiorstwie korzyści te przejawiają się w szybszym uruchamianiu produkcji, dłuższym czasie projektowania i analizy oraz zwiększonej elastyczności metod.
To rozwiązanie zapewnia:
- Lepsze zapewnienie jakości, dzięki czemu MPC może mieć pewność, że części zostaną uformowane zgodnie z wymaganiami, przed przekazaniem próbek klientowi.
- Eliminację wielu dodatkowych kontroli wymiarowych, co pozwala na szybsze zablokowanie narzędzi i procesów do produkcji.
- Zwiększoną elastyczność inspekcji, która zapewnia ocenę większej liczby opcji produkcyjnych i więcej czasu na projektowanie i testowanie form, co przekłada się bezpośrednio na nową przewagę konkurencyjną MPC — lepsze części w krótszym czasie i bardziej zadowoleni klienci.
- Krótszy czas wprowadzenia na rynek, podczas gdy konkurenci tracą dnie lub tygodnie na inspekcje sondą stykową, MPC gromadzi od 500 000 do ponad miliona punktów na powierzchni w ciągu kilku minut.
- Zwiększona zdolność do penetracji nowych rynków. MPC przeskoczyła od ściśle funkcjonalnych, rzadko oglądanych części do wysoce skomplikowanych, widocznych dla nabywcy pokryw silnika.
